Гидрокрекинг – играет ведущую роль в производстве топлив с высокий полнотой сгорания, экономичного сырья для нефтехимических производств и качественных смазочных материалов. Только путём гидрокрекинга можно преобразовать компоненты тяжелого нефтяного топлива в моторные топлива и смазочные материалы, качество которых не отстаёт от всё более высоких экологических требований и запросов рынка.
Процесс гидрокрекинга позволяет перерабатывать различные фракции нефти и давать почти любой целевой продукт с молекулярной массой ниже, чем у сырья. Одновременно почти полностью удаляются примеси, содержащие серу, азот и кислород, и происходит насыщение олефинов, так что продукты представляют собой смесь практически чистых парафинов, нафтенов и ароматических углеводородов. Широкий спектр применений процесса гидрокрекинга иллюстрирует табл. 1.
Применение процесса гидрокрекинга
№ | Сырьё | Продукт |
1 | Бензиновые фракции | Пропан и бутан |
2 | Керосин | Бензиновые фракции |
3 | Дизельные фракции прямой перегонки | Бензиновые фракции и/или авиационное топливо |
4 | Атмосферный газойль | Бензиновые фракции, авиационное топливо и/или дистилляты |
5 | Конденсаты природных газов | Бензиновые фракции |
6 | Вакуумные газойли | Бензиновые фракции, авиационное топливо, дистилляты, смазочные масла |
7 | Деасфальтированные и деметаллизированные остатки нефти | Бензиновые фракции, авиационное топлива, дистилляты, смазочные масла |
8 | Остатки атмосферной перегонки нефти | Бензиновые фракции, дистилляты, вакуумные газойли и низкосернистое остаточное топливо |
9 | ЛГ каталитического крекинга | Бензиновые фракции |
10 | ТГ каталического крекинга | Бензиновые фракции и/или дистилляты |
11 | Дистиллят коксования | Бензиновые фракции |
12 | ТГ коксования | Бензиновые фракции и/или дистилляты |
Реакция гидрокрекинга заключается в разрыве длинных цепочек углеводородов при помощи высоких температур и катализатора с последующим присоединением водорода к местам разрыва связей. Таким образом, из тяжелого углеводорода с содержанием большой доли примесей получают более легкие очищенные углеводороды.
В ходе гидрокрекинга неизбежно протекают реакции гидроочистки, удаления примесей из углеводородных цепочек. Ниже представлены основные реакции этого процесса.
- Реакция гидрообессеривания
При реакциях гидрообессеривания происходит образование углеводорода и сероводорода. Впоследствии сероводород удаляется из отходящих газов реактора, оставляя в конечной смеси только углеводороды. Реакции гидрообессеривания экзотермические, т.е. идут с выделением тепла. Меркаптаны, сульфиды и дисульфиды легко вступают в реакцию с образованием соответствующих насыщенных или ароматических соединений. Наиболее трудно удалить из сырья серу, входящую в состав циклических ароматических соединений, таких как тиофен.
Меркаптаны:
R -SH + H2 → R — H + H2S;
Сульфиды:
R — S – R + 2H2 → 2R — H + H2S;
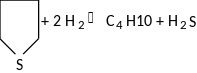
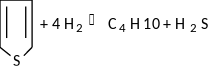
Скорость реакций гидрообессеривания увеличивается в результате:
R – NH2 + H2 → RH + NH3
Реакции гидрирования азотсодержащих соединений протекают медленнее, чем реакции гидрообессеривания.
Скорость реакций гидроодеазотирования увеличивается в результате:
- увеличения температуры;
- увеличения давления, в частности парциального давления водорода;
- использования специального катализатора.
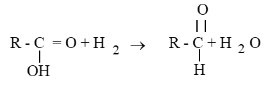
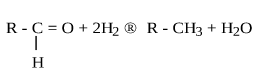
Реакции гидрирования кислородсодержащих соединений протекают легче, чем реакции гидрирования азотсодержащих соединений, с выделением тепла.
Эти реакции протекают с выделением очень большого количества тепла. Олефины и диолефины превращаются в насыщенные соединения. Скорость гидрогенизации олефинов и диолефинов выше, чем скорость реакции гидрогенизационной сероочистки.
R — CH = CH2 + H2 → R — CH2 — CH3
Помимо реакций гидроочистки протекают реакции гидрокрекинга.
- Гидроизомеризация, а затем крекинг с образованием более легких изопарафинов.
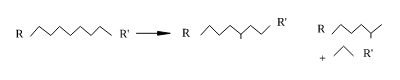
- Моноциклические нафтены деалкилируются, а затем изомеризуются с образованием легких изопарафинов, а также нафтенов с меньшим молекулярным весом.
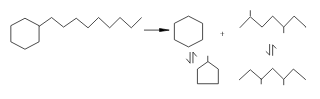
- Реакция бициклических нафтенов протекает с разрывом одного кольца, что сопровождается образованием алкилзамещенных моноциклических нафтенов, которые затем взаимодействуют по реакции, описанной в п. 2.
- Алкилбензолы деалкилируются с образованием ароматических соединений и изопарафинов. Они также подвергаются гидрогенизации с образованием моноциклических нафтенов, которые взаимодействуют по реакциям, описанным в п. 2.
- Реакции с участием бензонафтенов протекают, главным образом, с разрывом нафтеновых колец и образованием алкилбензолов, которые затем взаимодействуют по реакциям, описанным в п. 4. Они также могут подвергаться гидрогенизации бензольного кольца с образованием бициклических нафтенов, которые затем взаимодействуют по реакциям, описанным в п. 3.
- Полиароматические соединения сначала подвергаются реакции гидрогенизации одного кольца с образованием бензонафтенов. Затем бензонафтены взаимодействуют по реакциям, описанным в п. 5.
Катализаторы реакции гидрокрекинга
Катализатор, используемый при гидрокрекинге, обычно относится к типу (Ni-Co-Fe), (Mo-W-U) на подложке из окиси кремния/алюминия. Соотношение оксида алюминия к оксиду кремния используется для контроля степени гидрокрекинга, гидродеалкилирования, гидроизомеризации и гидродециклизации. Реакции крекинга усиливаются с увеличением содержания оксида кремния в катализаторе. Металлы в форме сульфидов контролируют десульфурацию, денитрификацию и гидрирование олефинов, ароматических соединений и тому подобного.
Выбор каталитической системы зависит от обрабатываемого сырья и требуемых продуктов. В большинстве случаев подходящую систему получают путем использования двух или более катализаторов с различными показателями кислотности и гидрирования. Реактор может также содержать небольшое количество (до 10%) катализатора десульфуризации и денитрификации в последнем слое реактора.
Конфигурация процесса
Установки гидрокрекинга могут работать в следующих возможных режимах: одноступенчатый (однократный режим), одноступенчатый режим с частичной или полной рециркуляцией и двухступенчатый режим. Эти режимы работы показаны на рис. 1-2.
Выбор конфигурации процесса зависит от каталитической системы. Основными параметрами, которые необходимо учитывать, являются качество исходного сырья, тип и требуемые качества продукта, а также инвестиционные и эксплуатационные расходы установки.
Одноступенчатый режим
Этот режим работы оказывает большое влияние на качество и выход продукта. Одноступенчатый режим дает около 0,3 барреля нафты на каждый баррель среднего дистиллята. Одноступенчатая схема адаптирована для преобразования вакуумного газойля в средний дистиллят и обеспечивает высокую селективность. Конверсия обычно составляет около 50-60%. Необработанный материал имеет низкое содержание серы, азота и других примесей и используется либо в качестве сырья для установок жидкостного каталитического крекинга (FCCU), либо в качестве компонента для смешивания с мазутом.
Одноступенчатый режим может осуществляться с частичной или полной рециркуляцией непереработанного остатка. При полной рециркуляции выход нафты составляет примерно 0,45 барреля на баррель продуктов среднего дистиллята. Режим частичной рециркуляции предпочтительнее полной рециркуляции, поскольку последняя приводит к накоплению неперерабатываемого материала при подаче в установку, что приводит к более высокой скорости загрязнения катализатора.
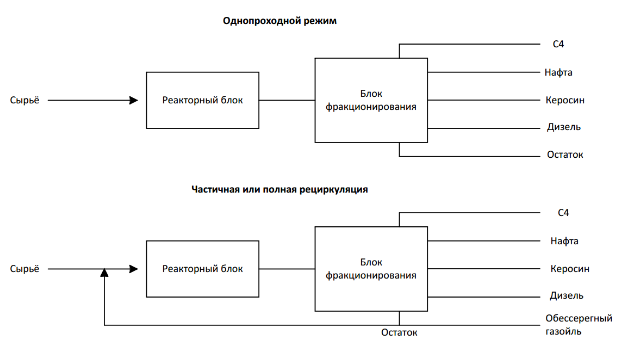
Рисунок 1 – одноступенчатый режим
Двухступенчатый режим
В двухступенчатой схеме не переработанный материал с первой ступени поступает на вторую установку гидрокрекинга. В этом случае сырьё для второй ступени уже очищено от серы, азота и других примесей, и установка второй ступени может переработать больший процент сырья с лучшим качеством продукта.
Сырье для тяжелого газойля содержит некоторое количество высококипящих ароматических молекул. Они тяжело подвергаются процессу крекинга, и при переработке сырья, как правило, концентрируются в аппаратах установки. Высокая концентрация этих молекул увеличивает скорость загрязнения катализатора. Поэтому в двухступенчатой схеме для первой ступени не предусмотрен возврат непревращенного остатка в реакцию, следовательно, концентрация ароматических молекул не растёт, поскольку нет рециркуляции. Первая ступень также снижает концентрацию этих молекул в сырье для второй ступени, следовательно, на второй ступени, также наблюдается более низкая концентрация высококипящих ароматических молекул.
При двухступенчатом режиме работы образуется меньше легких газов и расходуется меньше водорода на баррель сырья. Как правило, наилучшие качества продукта (наименьшее содержание меркаптанов, самая высокая температура дымления и самая низкая температура застывания) получаются на второй стадии. При этом качество первой ступени значительно хуже второй. Комбинированный продукт двух ступеней аналогичен продукту одной ступени с рециркуляцией при том же качестве сырья.
Двухступенчатая схема позволяет более гибко регулировать рабочие условия, а распределение между нафтой и средним дистиллятом является более гибким. По сравнению с одноступенчатой схемой частичной/полной рециркуляции двухступенчатая схема требует более высоких инвестиций, но, в целом, является более экономичной.
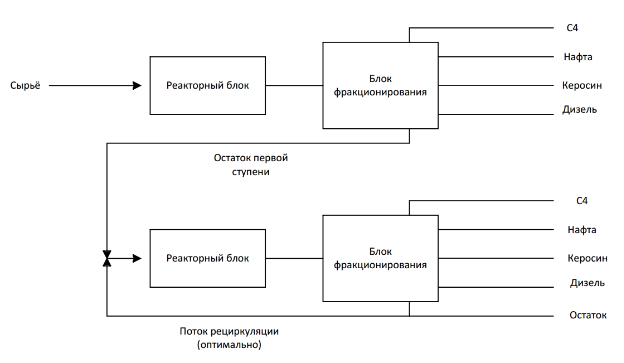
Рисунок 2 – двухступенчатый режим
Детальное описание технологической схемы
Подача сырья в реакторный блок состоит из двух или более потоков (см. рис. 3). Один поток представляет собой вакуумный газойль (VGO), подаваемый из резервуара для хранения, а другой поток может представлять собой VGO непосредственно из установки вакуумной дистилляции. Кроме того, может быть дополнительный рециркулирующий поток, состоящий из непереработанного остатка с куба фракционирующей колонны. Комбинированное сырье фильтруется в фильтрах F-01 для удаления большей части твердых частиц, которые могут засорить слои катализатора и привести к проблемам с перепадом давления в реакторе. После того, как сырьё прошло через емкость V-07, оно нагнетается до давления в системе реактора питающим насосом P-01.
Обогащенный водородом рециркуляционный газ от компрессора С-01 объединяется с подачей сырья перед теплообменниками Е-02. Поток нефтяного газа затем проходит через трубное пространство теплообменника Е-02, где он нагревается путем обмена с горячим выходным потоком реактора. Ниже по потоку от теплообменников подачи отходящих газов смесь дополнительно нагревается в реакционной печи H-01. Температура на входе в реактор контролируется регистратором и контроллером температуры путем управления подачей топлива через горелки в печь.
Подпиточный водород нагревается в трубном пространстве теплообменника E-01 выходящим из реактора потоком. Этот подпиточный водород затем поступает в реактор. Реактор гидрокрекинга V-01, как правило, представляет собой реактор бутылочного типа. Подпиточный водород после предварительного нагрева в теплообменниках E-01 поступает через реактор в кольцевое пространство между внешней оболочкой реактора и внутренней его частью. Подпиточный водород компенсирует долю водорода в рециркуляционном газе так как он расходуется в ходе реакций гидроочистки и гидрокрекинга, а также предотвращает накопление сероводорода. Доля Н2 в составе рециркуляционного газа также может уменьшатся вследствие образования лёгких парафинов (С1 – С4), тем самым снижая парциальное давление водорода. Поэтому на производстве часть рециркуляционного газа сбрасывают на факел, контролируя концентрацию Н2, и подпитывают систему свежим водородом.
После того, как подпиточный водород прошел вверх через реактор, он соединяется с рециркулируемым газом и нагретым сырьём, подаваемым от реакционной печи. Затем горячая реакционная смесь проходит через реактор. Холодный охлаждающий газ от рециркуляционного компрессора С-01 подается в реактор между слоями катализатора, чтобы ограничить повышение температуры, вызванное экзотермическими реакциями.
Реактор разделен на несколько неравных слоев катализатора. Это делается для того, чтобы обеспечить примерно одинаковое повышение температуры в каждом слое катализатора и ограничить повышение температуры до 260 0С. Таким образом, первый и второй слои могут содержать 10 и 15% от общего количества катализатора, в то время как третий и четвертый слои содержат 30 и 45% от общего количества катализатора.
Внутренние части реактора расположены между слоями катализатора так, чтобы обеспечить тщательное перемешивание реагентов с закалкой и обеспечить хорошее распределение газа и жидкости, поступающих в каждый слой. Правильное распределение реагентов имеет первостепенное значение для предотвращения горячих точек и увеличения срока службы катализатора.
Непосредственно под впускным патрубком реактора находится конус распределенной подачи. Эти внутренние элементы способствуют распределению потока сырья и улавливают мусор, попадающий в реактор. Под входной корзиной поток сырья проходит через перфорированную пластину и распределительный лоток для дальнейшего распределения перед поступлением в первый слой катализатора.
Внутреннее оборудование, находящееся между слоями катализатора, состоит из:
- опорной решетки катализатора, которая поддерживает катализатор в первом слое, покрыта проволочным экраном;
- закалочного кольца, которое рассеивает газ в горячей реакционной смеси с верхнего слоя;
- перфорированной пластины для равномерного распределения охлажденной реакционной смеси;
- распределительного лотка для окончательного распределения охлажденной реакционной смеси перед ее поступлением в следующий слой катализатора;
- дренажной трубы для катализатора, которая проходит через промежуточные элементы и соединяет каждый слой катализатора с нижним слоем.
Выгрузку отработанного катализатора выполняют через сопло для слива катализатора, предусмотренное в нижней части реактора. Затем каждый слой стекает в следующий нижний слой через дренажную трубу слоя, так что почти весь катализатор может быть удалена из реактора с минимальными усилиями.
Индикаторы перепада давления предназначены для непрерывного измерения перепада давления в верхних слоях катализатора и во всем реакторе. Повышение данного параметра может свидетельствовать о загрязнении или повреждении слоёв катализатора.
Реактор снабжен термопарами, расположенными таким образом, чтобы можно было наблюдать температуру катализатора как по оси, так и по окружности. Термопары расположены в верхней и нижней части каждого слоя. Высокая температура в одной точке католического слоя свидетельствует о том, что реакционная смесь не проходит сквозь слой равномерно вследствии чего качество реакции будет ухудшено. Причинами этого могут быть не качественное заполнение реактора катализатором или нарушение ведения технологического процесса во время пусковых операций.
Сепаратор высокого давления
Температура сепаратора высокого давления V-02 регулируется примерно на уровне 7600С с помощью регулятора температуры, который регулирует частоту вращения вентиляторов воздухоохладителя Е-04. Температура сепаратора тщательно контролируется, чтобы температура абсорбера H2S, находящегося ниже по потоку, не колебалась, так как чистота водорода значительно ниже при более высоких температурах.
Однако при более низкой температуре в барабане сепаратора происходит плохое разделение углеводородов и воды.
Сепаратор низкого давления
Жидкость из сепаратора V-02 сбрасывает давление через клапан регулирования уровня сепаратора высокого давления V-02 и подается в сепаратор низкого давления V-06. Верхние пары сепаратора низкого давления поступают в аминовый сепаратор V-05. Поток углеводородов, выходящий из сепаратора, подается в сепаратор очистки H2S V-04. Кислую воду, отобранную из сепаратора низкого давления, направляют на очистные сооружения кислой воды.
Абсорбер рециркуляционного газа
Абсорбция DEA (диэтаноламина) V-04 используется для удаления H2S из рециркулируемого газа. Газ H2S поглощается раствором DEA из-за химической реакции DEA с H2S. Количество H2S, которое может вступить в реакцию, зависит от условий эксплуатации.
Низкая температура, высокое давление и высокая концентрация H2S в абсорбере V-04 улучшает реакции. В установках регенерации DEA высокая температура и низкое давление используются для обратного хода реакции и удаления H2S из раствора DEA.
Около 90% H2S, образующегося в результате реакций десульфуризации, удаляется из рециркулируемого газа в абсорбере путем очистки газа водным раствором диэтаноламина. Абсорбер представляет собой вертикальный сосуд, заполненный балластными кольцами из нержавеющей, стали. Рециркулированный газ проходит через опорную пластину и поднимается вверх через насадку. Обедненный раствор DEA из регенератора DEA поступает в верхнюю часть абсорбера через впускной распределитель и течет вниз через насадку. Насыщенный DEA со дна абсорбера направляется в блок рекуперации H2S.
Компрессор рециркуляционного газа
Рециркулированный газ циркулирует с помощью компрессора рециркулирующего газа С-01, приводимого в действие паровой турбиной. Наибольшая часть потока рециркулируемого газа присоединяется к потоку подачи сырья перед теплообменниками. Часть газового потока из рециркуляционного компрессора поступает при регулировании температуры на слоях катализатора.
Подача сырья в реакторный блок состоит из двух или более потоков (см. рис. 3). Один поток представляет собой вакуумный газойль (VGO), подаваемый из резервуара для хранения, а другой поток может представлять собой VGO непосредственно из установки вакуумной дистилляции. Кроме того, может быть дополнительный рециркулирующий поток, состоящий из непереработанного остатка с куба фракционирующей колонны. Комбинированное сырье фильтруется в фильтрах F-01 для удаления большей части твердых частиц, которые могут засорить слои катализатора и привести к проблемам с перепадом давления в реакторе. После того, как сырьё прошло через емкость V-07, оно нагнетается до давления в системе реактора питающим насосом P-01.
Обогащенный водородом рециркуляционный газ от компрессора С-01 объединяется с подачей сырья перед теплообменниками Е-02. Поток нефтяного газа затем проходит через трубное пространство теплообменника Е-02, где он нагревается путем обмена с горячим выходным потоком реактора. Ниже по потоку от теплообменников подачи отходящих газов смесь дополнительно нагревается в реакционной печи H-01. Температура на входе в реактор контролируется регистратором и контроллером температуры путем управления подачей топлива через горелки в печь.
Подпиточный водород нагревается в трубном пространстве теплообменника E-01 выходящим из реактора потоком. Этот подпиточный водород затем поступает в реактор. Реактор гидрокрекинга V-01, как правило, представляет собой реактор бутылочного типа. Подпиточный водород после предварительного нагрева в теплообменниках E-01 поступает через реактор в кольцевое пространство между внешней оболочкой реактора и внутренней его частью. Подпиточный водород компенсирует долю водорода в рециркуляционном газе так как он расходуется в ходе реакций гидроочистки и гидрокрекинга, а также предотвращает накопление сероводорода. Доля Н2 в составе рециркуляционного газа также может уменьшатся вследствие образования лёгких парафинов (С1 – С4), тем самым снижая парциальное давление водорода. Поэтому на производстве часть рециркуляционного газа сбрасывают на факел, контролируя концентрацию Н2, и подпитывают систему свежим водородом.
После того, как подпиточный водород прошел вверх через реактор, он соединяется с рециркулируемым газом и нагретым сырьём, подаваемым от реакционной печи. Затем горячая реакционная смесь проходит через реактор. Холодный охлаждающий газ от рециркуляционного компрессора С-01 подается в реактор между слоями катализатора, чтобы ограничить повышение температуры, вызванное экзотермическими реакциями.
Реактор разделен на несколько неравных слоев катализатора. Это делается для того, чтобы обеспечить примерно одинаковое повышение температуры в каждом слое катализатора и ограничить повышение температуры до 260 0С. Таким образом, первый и второй слои могут содержать 10 и 15% от общего количества катализатора, в то время как третий и четвертый слои содержат 30 и 45% от общего количества катализатора.
Внутренние части реактора расположены между слоями катализатора так, чтобы обеспечить тщательное перемешивание реагентов с закалкой и обеспечить хорошее распределение газа и жидкости, поступающих в каждый слой. Правильное распределение реагентов имеет первостепенное значение для предотвращения горячих точек и увеличения срока службы катализатора.
Непосредственно под впускным патрубком реактора находится конус распределенной подачи. Эти внутренние элементы способствуют распределению потока сырья и улавливают мусор, попадающий в реактор. Под входной корзиной поток сырья проходит через перфорированную пластину и распределительный лоток для дальнейшего распределения перед поступлением в первый слой катализатора.
Внутреннее оборудование, находящееся между слоями катализатора, состоит из:
- опорной решетки катализатора, которая поддерживает катализатор в первом слое, покрыта проволочным экраном;
- закалочного кольца, которое рассеивает газ в горячей реакционной смеси с верхнего слоя;
- перфорированной пластины для равномерного распределения охлажденной реакционной смеси;
- распределительного лотка для окончательного распределения охлажденной реакционной смеси перед ее поступлением в следующий слой катализатора;
- дренажной трубы для катализатора, которая проходит через промежуточные элементы и соединяет каждый слой катализатора с нижним слоем.
Выгрузку отработанного катализатора выполняют через сопло для слива катализатора, предусмотренное в нижней части реактора. Затем каждый слой стекает в следующий нижний слой через дренажную трубу слоя, так что почти весь катализатор может быть удалена из реактора с минимальными усилиями.
Индикаторы перепада давления предназначены для непрерывного измерения перепада давления в верхних слоях катализатора и во всем реакторе. Повышение данного параметра может свидетельствовать о загрязнении или повреждении слоёв катализатора.
Реактор снабжен термопарами, расположенными таким образом, чтобы можно было наблюдать температуру катализатора как по оси, так и по окружности. Термопары расположены в верхней и нижней части каждого слоя. Высокая температура в одной точке католического слоя свидетельствует о том, что реакционная смесь не проходит сквозь слой равномерно вследствии чего качество реакции будет ухудшено. Причинами этого могут быть не качественное заполнение реактора катализатором или нарушение ведения технологического процесса во время пусковых операций.
Сепаратор высокого давления
Температура сепаратора высокого давления V-02 регулируется примерно на уровне 7600С с помощью регулятора температуры, который регулирует частоту вращения вентиляторов воздухоохладителя Е-04. Температура сепаратора тщательно контролируется, чтобы температура абсорбера H2S, находящегося ниже по потоку, не колебалась, так как чистота водорода значительно ниже при более высоких температурах.
Однако при более низкой температуре в барабане сепаратора происходит плохое разделение углеводородов и воды.
Сепаратор низкого давления
Жидкость из сепаратора V-02 сбрасывает давление через клапан регулирования уровня сепаратора высокого давления V-02 и подается в сепаратор низкого давления V-06. Верхние пары сепаратора низкого давления поступают в аминовый сепаратор V-05. Поток углеводородов, выходящий из сепаратора, подается в сепаратор очистки H2S V-04. Кислую воду, отобранную из сепаратора низкого давления, направляют на очистные сооружения кислой воды.
Абсорбер рециркуляционного газа
Абсорбция DEA (диэтаноламина) V-04 используется для удаления H2S из рециркулируемого газа. Газ H2S поглощается раствором DEA из-за химической реакции DEA с H2S. Количество H2S, которое может вступить в реакцию, зависит от условий эксплуатации.
Низкая температура, высокое давление и высокая концентрация H2S в абсорбере V-04 улучшает реакции. В установках регенерации DEA высокая температура и низкое давление используются для обратного хода реакции и удаления H2S из раствора DEA.
Около 90% H2S, образующегося в результате реакций десульфуризации, удаляется из рециркулируемого газа в абсорбере путем очистки газа водным раствором диэтаноламина. Абсорбер представляет собой вертикальный сосуд, заполненный балластными кольцами из нержавеющей, стали. Рециркулированный газ проходит через опорную пластину и поднимается вверх через насадку. Обедненный раствор DEA из регенератора DEA поступает в верхнюю часть абсорбера через впускной распределитель и течет вниз через насадку. Насыщенный DEA со дна абсорбера направляется в блок рекуперации H2S.
Компрессор рециркуляционного газа
Рециркулированный газ циркулирует с помощью компрессора рециркулирующего газа С-01, приводимого в действие паровой турбиной. Наибольшая часть потока рециркулируемого газа присоединяется к потоку подачи сырья перед теплообменниками. Часть газового потока из рециркуляционного компрессора поступает при регулировании температуры на слоях катализатора.
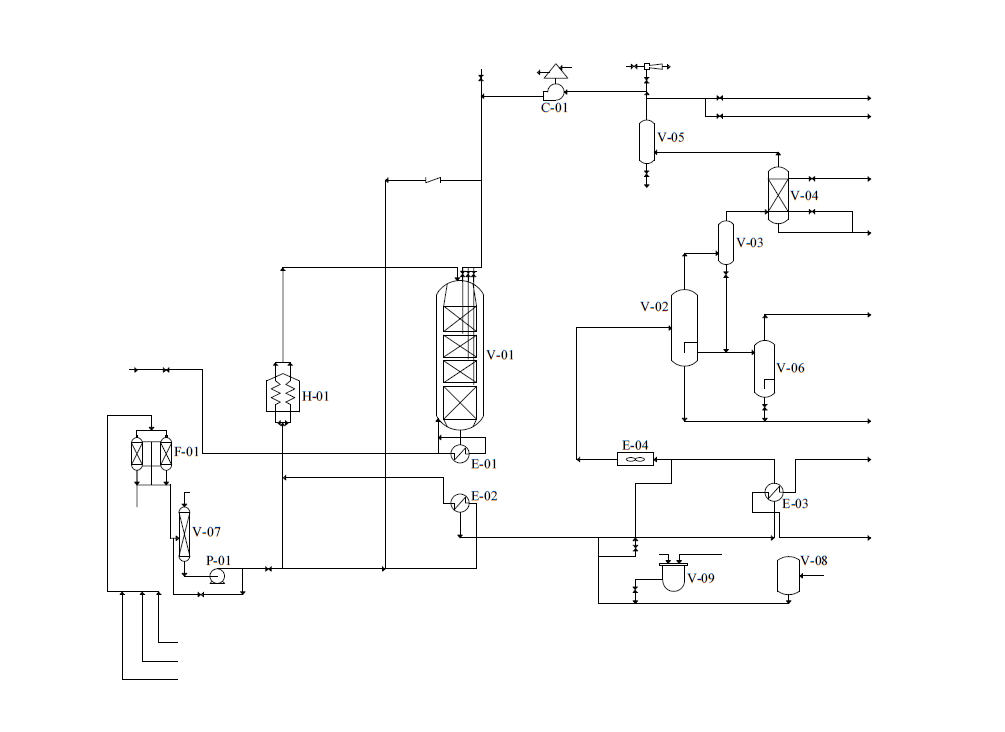
Рисунок 3 – Технологическая схема установки гидрокрекинга
F-01 – питательный фильтр; V-07– сырьевая ёмкость; P-01 – питательный насос; H-01 – реакционная печь; V-01 – реактор гидрокрекинга; E-02 – подогреватель исходного сырья; E-01 – подогреватель подпиточного водорода; C-01 – рециркуляционный компрессор; V-03, V-05 – аминовые сепараторы; V-04 – сепаратор очистки сероводорода; V-02 – сепаратор высокого давления; V-06 – сепаратор низкого давления; E-04 – воздушный холодильник; E-03 – теплообменник кубового продукта/обессеренного сырья; V-09 – полисульфидная ёмкость; V-08 – нагнетательная ёмкость воды.